Comparative Analysis of Spherical Nickel Powder vs. Other Nickel Powder Forms
Introduction:
Nickel powder is a versatile material with various forms, each exhibiting distinct properties that cater to specific applications. In this article, we delve into the comparative analysis of spherical nickel powder against other nickel powder forms, evaluating their performance across different industries and applications.
Understanding Nickel Powder Forms:
Nickel powder is available in multiple forms, including irregular, dendritic, and spherical. Each form undergoes unique production processes, resulting in diverse particle shapes and characteristics.
Irregular Nickel Powder:
Irregular nickel powder, with its non-uniform particle shape, finds applications in industries where precise control over particle morphology is not critical. It is often utilized in traditional metallurgical processes, such as powder metallurgy and sintering.
Dendritic Nickel Powder:
Dendritic nickel powder exhibits a tree-like structure and is valued for its high surface area. This form is commonly used in applications where increased surface contact is advantageous, such as in electrochemical and catalytic processes.
Spherical Nickel Powder:
Spherical nickel powder stands out due to its uniform, rounded particle shape. The spherical morphology is achieved through advanced manufacturing techniques, resulting in tightly controlled particle sizes. This form is particularly prized for its flowability, compressibility, and packing characteristics.
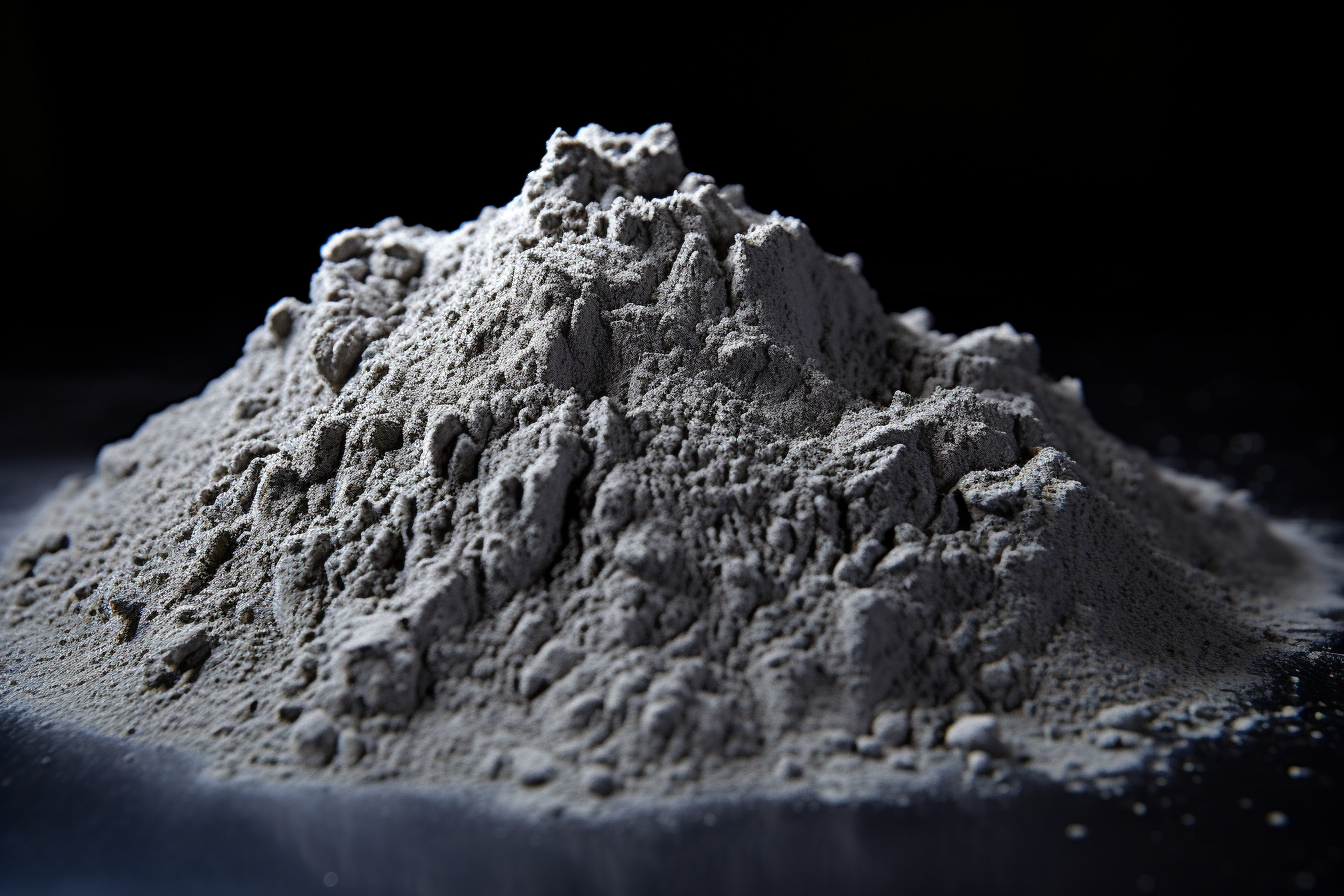
Comparative Performance Analysis:
a. Flowability and Packing:
Spherical nickel powder excels in flowability and packing density compared to irregular and dendritic forms. The spherical shape allows particles to move more freely, ensuring better packing in various applications, including powder metallurgy and additive manufacturing.
b. Surface Area and Reactivity:
Dendritic nickel powder boasts a higher surface area due to its intricate structure, making it suitable for catalytic applications. However, the spherical nickel powder strikes a balance between surface area and particle uniformity, offering advantages in applications like catalysis and electrochemistry.
c. Powder Metallurgy and Additive Manufacturing:
Spherical nickel powder showcases superior performance in powder metallurgy and additive manufacturing processes. Its uniformity and flowability contribute to enhanced sintering properties, resulting in denser and more reliable components compared to irregular or dendritic counterparts.
d. Conductive Inks and Electronics:
In electronic applications, spherical nickel powder is often preferred for its excellent conductivity and uniform particle distribution. The spherical shape allows for better dispersion in conductive inks, contributing to improved printing and coating processes.
e. Mechanical Properties in Coatings:
Irregular nickel powder may be suitable for certain coating applications, but spherical nickel powder offers advantages in terms of mechanical properties. Its uniform shape ensures consistent coating thickness, enhancing the overall quality and durability of coatings.
Conclusion:
While each form of nickel powder has its merits, the comparative analysis highlights the unique advantages of spherical nickel powder. Its superior flowability, packing density, and performance in powder metallurgy and additive manufacturing make it a preferred choice in various industries. Understanding the specific requirements of each application is c